Monitoring Process Definitions tab
The Monitoring Process Definitions are used to parameterize a specific Monitoring Process for materials based on a combination of their Customer Part Number, Location and Weight (or globally if none is specified in the Monitoring Process Definition). A Monitoring Process Definition configures the parameters of one Monitoring Process for specific types of materials. It is applied to a Monitoring Process when the Monitoring Process is started. The best fitting Monitoring Process Definition is selected based on the CustomerPartNumber, Location and Weight of the material. If any of those parameters are not specified for a Monitoring Process Definition, it can be applied for any material. If multiple Monitoring Process Definitions match the parameters of a material, the most specific Monitoring Process Definition is selected (see below).
|
Only one "default" Monitoring Process Definition can exist for a given tenant. This means, that if you have described a "default" process definition (a process definition without Customer Part Number, Location or Weight set), you cannot create a "default" process definition for another Process Name. |
Selection Process for the Monitoring Process Definitions
In case of multiple matching Monitoring Process Definitions, the following matching order is applied to select the most specific Monitoring Process Definition:
-
Definition matches the CustomerPartNumber, Location and Weight of the material.
-
Definition matches the CustomerPartNumber and Weight of the material (Definition has no Location specified).
-
Definition matches the CustomerPartNumber of the material (Definition has no Location and Weight specified).
-
Definition matches the Location and Weight of the material (Definition has no CustomerPartNumber specified).
-
Definition matches the Location of the material (Definition has no CustomerPartNumber and Weight specified).
-
Definition matches the Weight of the material (Definition has no CustomerPartNumber and Location specified).
-
Global Definition (neither CustomerPartNumber, Location nor Weight is specified) is used if one exists.
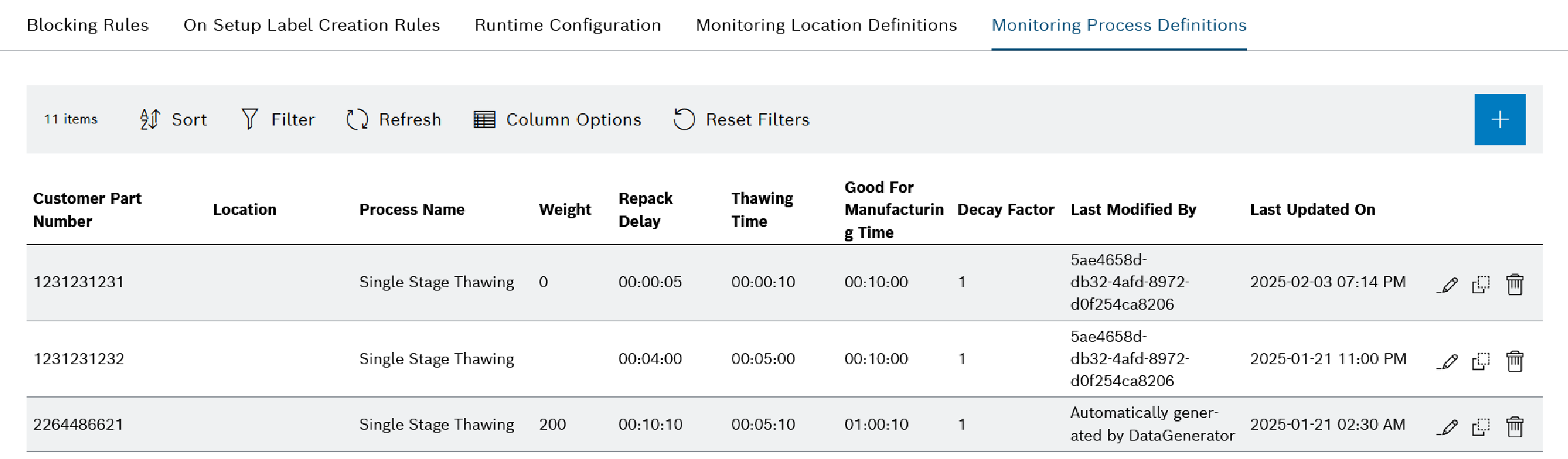
The monitoring process definitions are configured in the Monitoring Process Definitions tab under Material Management > Configuration.
Process Definitions
Element/icon | Description |
---|---|
Customer Part Number |
The Customer Part Number of the Material. |
Location |
The location where the material is scanned to start the Monitoring Process. Locations can be input in short or long and fixed or dotted notation. |
Process Name |
The Process Name this definition belongs to. (e.g. Single Stage Thawing). |
Weight |
The numeric value as printed on the material’s label (e.g. 1.5). |
Process-dependent configuration parameters |
Every monitoring process type has specific configuration parameters. These parameters are described in the process-specific documents below the section States and State Changes. |
Last Modified By |
|
Last Updated On |
|
Create and edit monitoring process definition
Prerequisite
MaterialManagement Expert
or MaterialManagement Administrator
role
Procedure
-
Open the Material Management > Configuration > Monitoring Process Definitions tab.
-
In the header, click on
to add a monitoring process definition.
Or:
Click on
to edit a monitoring process definition.
-
On the Create Monitoring Process Definition or Edit Monitoring Process Definition page, enter the desired conditions in the input and list fields.
-
Click on Add to create a Monitoring Process Definition. Or:
Click Save to accept the changes.
In the first step, a Process Name has to be selected. After selecting a Process Name the available parameters for the selected Monitoring Process will be displayed. Please refer to the process-specific pages below the section States and State Changes for descriptions of the parameters for every Monitoring Process.
Additionally, the parameters Customer Part Number, Location and Weight can be defined for every Monitoring Process Definition. These 3 parameters are not used by the Monitoring Process, but for the selection of the correct Monitoring Process Definition.
For example: If all materials with CustomerPartNumber 1000000000 need the same parameters for Single Stage Thawing, you could define a Monitoring Process Definition with only the Customer Part Number specified (Location and Weight empty) and have these parameters applied for all materials with this Customer Part Number.
If there is an exception where all materials with CustomerPartNumber 1000000000 and Weight 2.5 need a different set of parameters, an additional Monitoring Process Definition with CustomerPartNumber 1000000000 and Weight 2.5 (Location empty) could be added.The new or edited monitoring process definition appears in the table in the Configuration > Monitoring Process Definitions tab.
Clone monitoring process definition
Prerequisite
MaterialManagement Expert
or MaterialManagement Administrator
role
Procedure
-
Open the Material Management > Configuration > Monitoring Process Definitions tab.
-
To clone a monitoring process definition, click on
in the row containing the monitoring process definition.
-
In the Clone Monitoring Process Definition dialog window, enter the necessary information and click on add.
The blue info banner displays which fields need to be changed to avoid an ambiguous monitoring process definition.
The cloned monitoring process definition is displayed in the Monitoring Process Definitions tab.
Delete monitoring process definition
Prerequisite
MaterialManagement Administrator
role
Procedure
-
Open the Material Management > Configuration > Monitoring Process Definitions tab.
-
To delete a monitoring process definition, click on
in the row containing the monitoring process definition.
-
In the Delete Monitoring Process Definition dialog window, delete the monitoring process definition permanently with Delete.
The monitoring process definition is removed from the Monitoring Process Definitions tab.