View Supermarkets

The Supermarkets view is opened with . In the Supermarkets view, the supermarket and its components (modules, tracks and load units) can be configured and planned.
There are four areas in the Supermarkets view:
-
Header Supermarkets view
Refreshing the view, filtering by load unit, customizing the graphical display -
Graphical representation
Graphical view of the supermarket and its components -
Inventory area
Information on stocks, error messages -
Configuration Area
Configuration and planning of the supermarket and its components
Header Supermarkets view

Element/icon | Description |
---|---|
<Supermarket> |
Refresh supermarket view. |
Load units |
The load unit entered in the search is highlighted in light blue. |
|
Activate or deactivate live update. |
|
Show or hide load units in the graphical display. |
Loading side or Unloading side |
Select the perspectives of the graphical display:
|
Frontal or bird’s eye view |
Select the perspectives of the graphical display:
|
Graphical representation
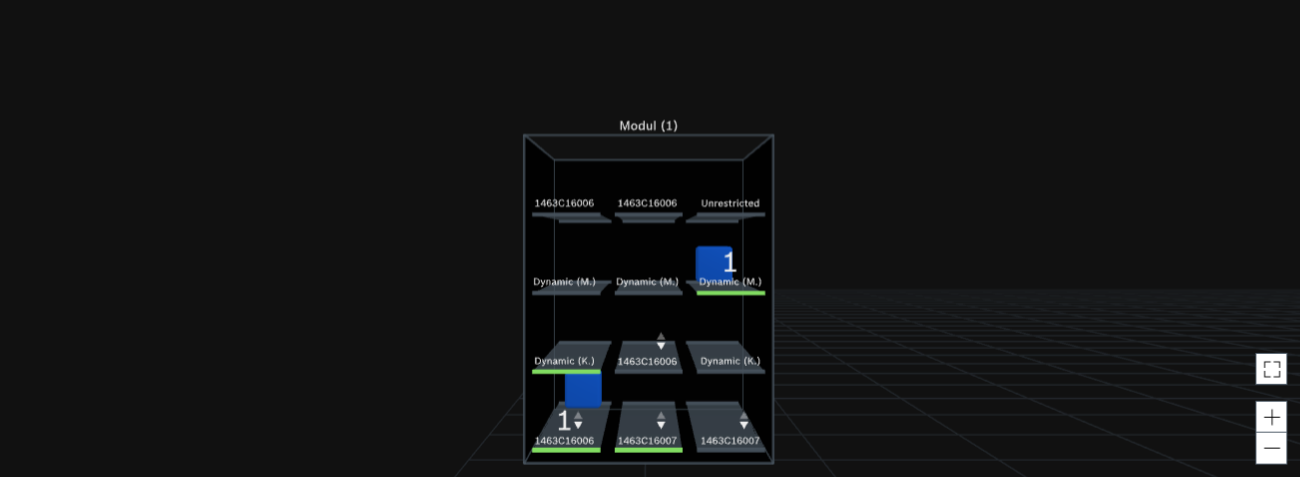
The graphic representation shows the supermarket with all modules, tracks/storage locations and load units.
A supermarket consists of any number of modules. Modules of the Shelf module type consist of any number of levels. The levels contain any number of tracks. Modules of the Surface module type consist of one level. The level contains any number of tracks or storage locations.
The representation of tracks and storage locations is identical. The graphical display is described below using the track. |
The graphic display view can be customized with the following buttons:
Button | Description | ||
---|---|---|---|
Zoom in or out.
|
|||
Switch to full-screen display. |
|||
Exit full-screen display.
|
The view or the section of the supermarket can be moved: To do this, place the mouse pointer in the required area and move the view or section by holding down the left mouse button. |
Information about load units and planning is displayed on the tracks:
-
The track shows the Kanban ID of the load unit.
-
The number on the track shows the current stock of load units.
-
White up arrow indicates that the maximum stock has been exceeded.
-
White down arrow indicates that the minimum stock has not been reached.
-
The green line on the track indicates the track that is currently being filled.
Color of the tracks and storage locations
Color | Description |
---|---|
Gray |
There are no track messages. |
Blue |
The track has been selected. |
Orange |
An error correction mode has been assigned to the track. |
Red |
Error message There is an error on the track. To view the error message in the stock area in the Errors tab, click the red track. |
Color of the load units
Color | Description |
---|---|
Transparent blue |
The load unit contains residual quantities. |
Blue |
The load unit is filled. |
Light blue |
The load unit has been selected. |
Gray |
Reserved space for a specific unit load. The space cannot be occupied by other unit loads. To see the transport order number, Kanban ID, material, and number of parts in the load unit in the configuration area, click the gray load unit. |
Yellow |
Warning Unknown carrier. To view the warning in the stock area in the Errors tab, click the yellow load unit. Entry deadline: Load unit expiration date‑Threshold value (days) warning has been reached. |
Red |
Error message Load unit was stored in the wrong track. To view the error message in the stock area in the Errors tab, click the red load unit. Entry deadline: Load unit expiration date‑Threshold value (days) error has been reached. |
Inventory area
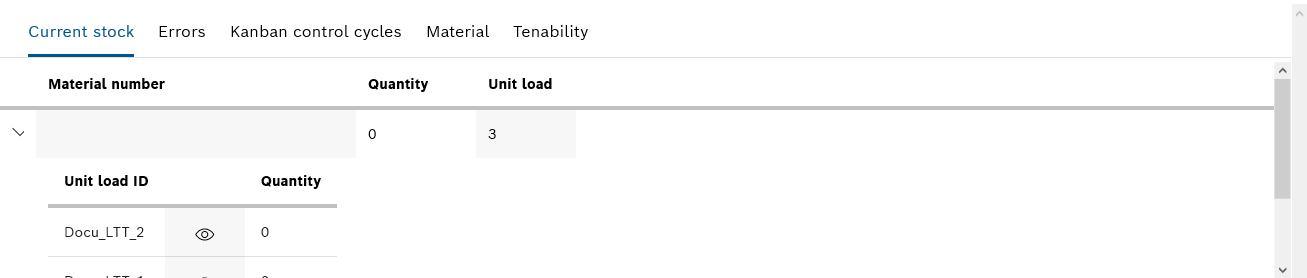
In the stock area, all information about the stored material in the supermarket is displayed under the tabs.
Element/icon | Description |
---|---|
|
Expand or retract the detailed view. |
In the graphical display, display tracks or load units in the bird’s eye view and highlight them in light blue. |
|
Delete row. |
Current stock tab
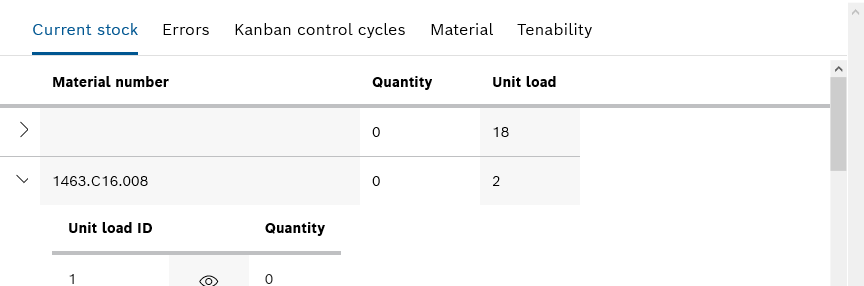
All materials, their load units and their number are listed in the Current stock tab. The detailed view shows the individual load units and their quantity.
Errors tab
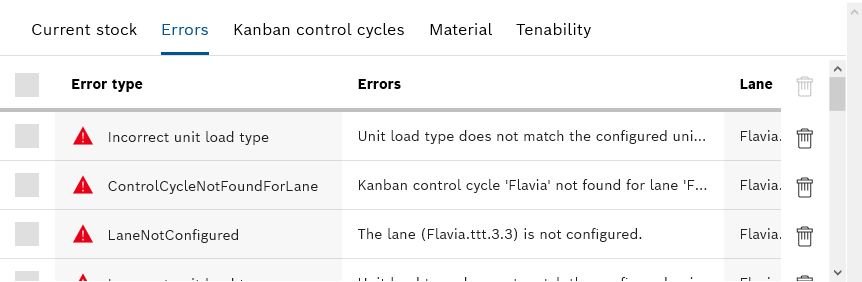
The Errors tab lists error messages for the supermarket. An error message consists of an error type and an error description. The error messages can include the track, storage location, material number, and Kanban ID.
Error messages can be deleted with . To delete multiple error messages at the same time, activate the checkboxes of the error messages and remove them in the header with
.
Before deleting an error message, verify that the error has been corrected. If an error has not been corrected, it will not be shown again after deletion and it is therefore not processed. |
Kanban control cycles tab
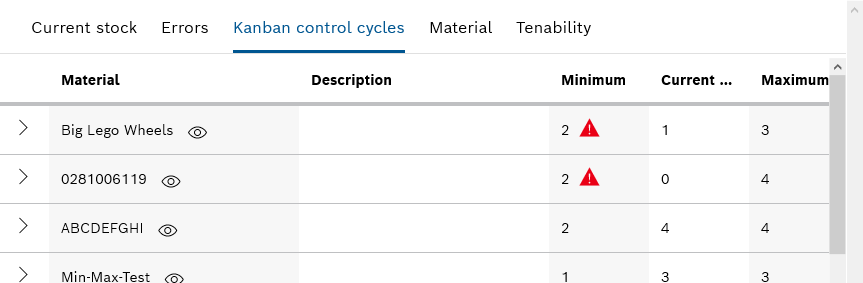
The Kanban control cycles tab lists the materials and their description. For each material, the specified minimum stock, the current stock, the maximum stock and the number of parts per container (PPCs) are displayed. The detailed view shows the track or storage location where the material is stored with the current material stock and its position.
Material tab
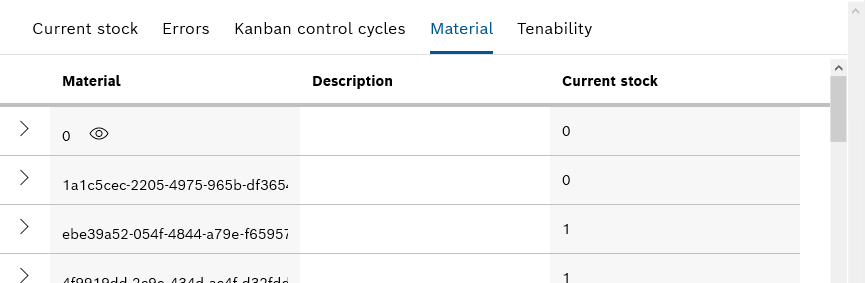
The Material tab lists the materials with their description and current stock. The detailed view shows the track or storage location where the material is stored current stock.
Configuration Area
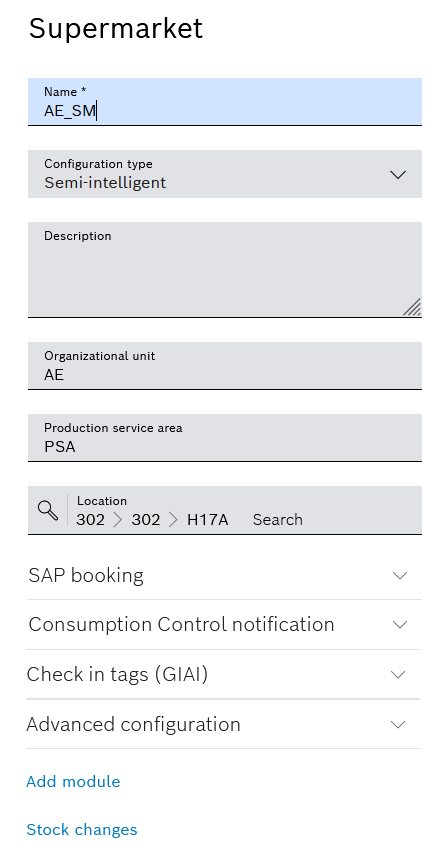
The configuration area is used to configure the supermarket and its components. The display depends on the selection in the graphical display:
-
Supermarket
No element is selected in the graphical display (click in the black area).
Overview: Supermarket Configuration Area -
Module
A module is selected in the graphical display.
Overview: Module Configuration Area -
Track or Storage location
A track or a storage location is selected in the graphical display.
Overview: Track/Storage Location Configuration Area -
Load units
A load unit is selected in the graphical display.
Overview: Load Unit Configuration Area
Overview: Supermarket Configuration Area
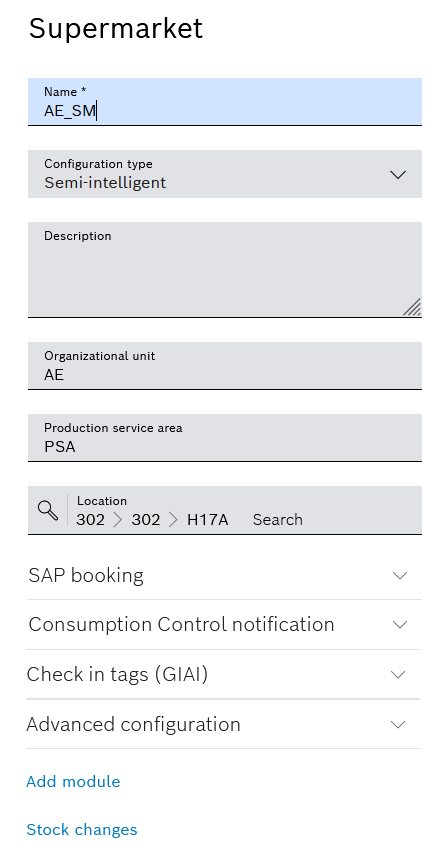
The supermarket configuration has identical effects on tracks and storage areas. The functions of the text boxes and drop-down lists are described below for the track as an example. |
Element/icon | Description | ||||||||||
---|---|---|---|---|---|---|---|---|---|---|---|
Name |
Name of the supermarket |
||||||||||
Configuration type |
Assign a supermarket to a configuration type. The drop-down list contains the following configuration types:
|
||||||||||
Description |
Description of the supermarket |
||||||||||
Organization unit |
Description of the organization, e.g. plant or area |
||||||||||
Production service area |
Description of the production unit, e.g. production service area (PSA) |
||||||||||
Location |
Define the Building , Hall and Station through which the supermarket can be supplied. |
||||||||||
SAP booking |
|
||||||||||
Consumption control message |
|
||||||||||
Check in (GIAI tag) |
Associates equipped with an RFID reader on their wrist can log in to the supermarket as soon as they begin work there. Using the RFID reader, the associate scans a GIAI tag, which is located at the corresponding positions (filling and removal side) of the supermarket. This makes it possible to tell where the load units are to be stored at any time.
|
||||||||||
Extended configuration |
|
||||||||||
Adding a Module |
Add a module to the supermarket. |
||||||||||
Stock Changes |
Display stock changes in the supermarket. |
||||||||||
Synchronize Kanban control cycles |
Synchronize Kanban control cycles with SAP. |
Overview: Module Configuration Area
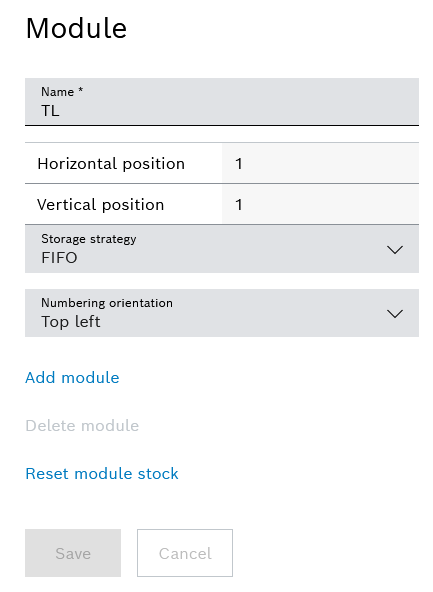
Element/icon | Description | ||
---|---|---|---|
Name |
Name of the module |
||
Horizontal position |
Horizontal position of the module from left to right (starting from the filling side)
|
||
Vertical position |
Vertical position of the module from bottom to top
|
||
Storage strategy |
Procedure for removal from the module
|
||
Numbering alignment |
|
||
Adding a Module |
Add a module to the supermarket. |
||
Deleting a Module |
Delete the module from the supermarket.
|
||
Reset module stock |
Delete all load units and materials for a module. |
Overview: Track/Storage Location Configuration Area
Modules with shelf module type consist of any number of levels with any number of tracks. Modules with a surface module type consist of one level with any number of tracks or storage locations.
The configuration area of a track and a storage location is identical. The configuration area is described below, using the track as an example. |
There are two tabs in the Track configuration area:
-
Details
Planning of the track (assignment of the load units, troubleshooting) -
Configuration
Configuration of the track (load units, visual tags)
Before editing the details, the track must be configured as the definition of the load unit types essential for the assignment mode. |
Track configuration area, tab details
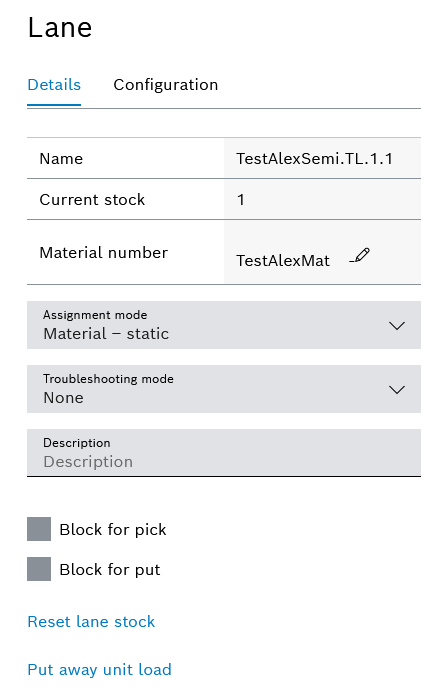
Element/icon | Description | ||
---|---|---|---|
Name |
Name of the track The name is made up as follows: <Name Supermarkt>.<Name Modul>.<Name Ebene*>.<Name Bahn**>
|
||
Current stock |
Number of load units on the track |
||
Material number |
Material number of the load units on the track Assign a Kanban control cycle to the material with |
||
Assignment mode |
Procedure for assigning load units to the track
|
||
Error correction mode |
While a supermarket is operating, the physical stock may differ from the digital stock. This stock deviation can be detected by the user or automatically. To correct the stock deviation, the following troubleshooting modes are selected:
|
||
Description |
Any text input. Issued as an ESL (electronic shelf label) tag on the item label of the material. |
||
|
Load units can or cannot be removed and booked out. |
||
|
Load units can or cannot be moved into stock and booked in. |
||
Re-set stock |
Delete all load units and materials of a track. |
||
Booking in a Load Unit |
Book load unit in on the track. |
Track configuration area, configuration tab
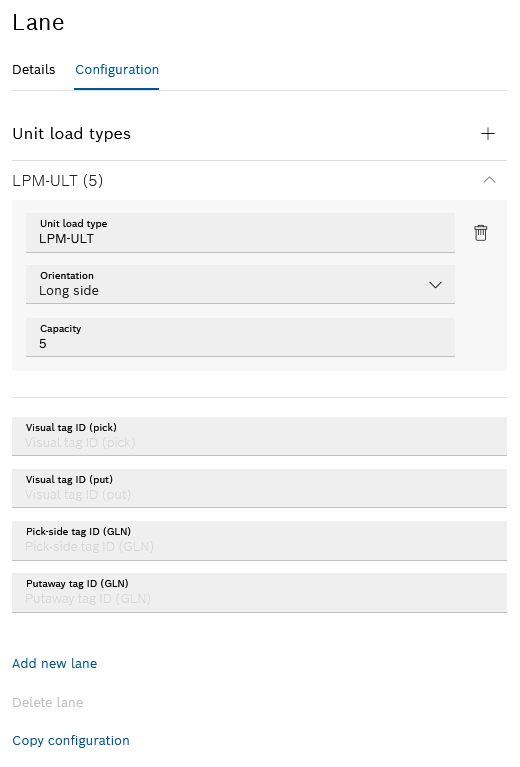
Element/icon | Description | ||
---|---|---|---|
Load unit types |
Add a load unit type to the track.
|
||
<Ladungsträgertyp> |
Information about the load unit type and track
If multiple load units are assigned to the track, and if no load units are booked in on the track, use |
||
Visual tag ID (removal) |
Identification number of the visual tag for the removal side |
||
Visual tag ID (filling) |
Identification number of the visual tag for the removal side |
||
Removal tag ID (GLN) |
Identification number of the removal tag in GLN format |
||
Filling tag ID (GLN) |
Identification number of the filling tag in GLN format |
||
Add new track |
Add a new track to the right of the highlighted track. |
||
Delete track |
Delete track from the module. |
||
Copy configuration |
Apply the configuration of the track for the entire module. |
Overview: Load Unit Configuration Area
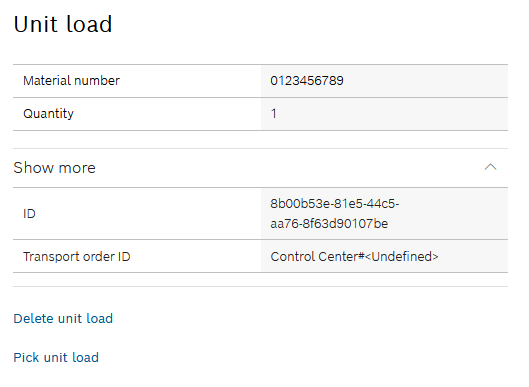
Element/icon | Description |
---|---|
Material number |
Material number of the material assigned to the load unit |
Quantity |
Number of load units on the track |
More details |
Details of the material |
Delete a load unit |
Remove the assignment of the load unit to the track. |
Remove a load unit |
Remove the load unit from the track. |