Product parts lists
All products that have a product parts list are displayed in Product parts lists. The associated product parts lists can be opened by selecting a product.
A product parts list is a structured arrangement of the individual components and materials of the product. The list of components and materials can be displayed by selecting a product parts list.
The products can be grouped under umbrella terms for greater clarity.
Group products and packaging specifications or change grouping
Any number of product parts lists can be created or imported for each product.
Example:
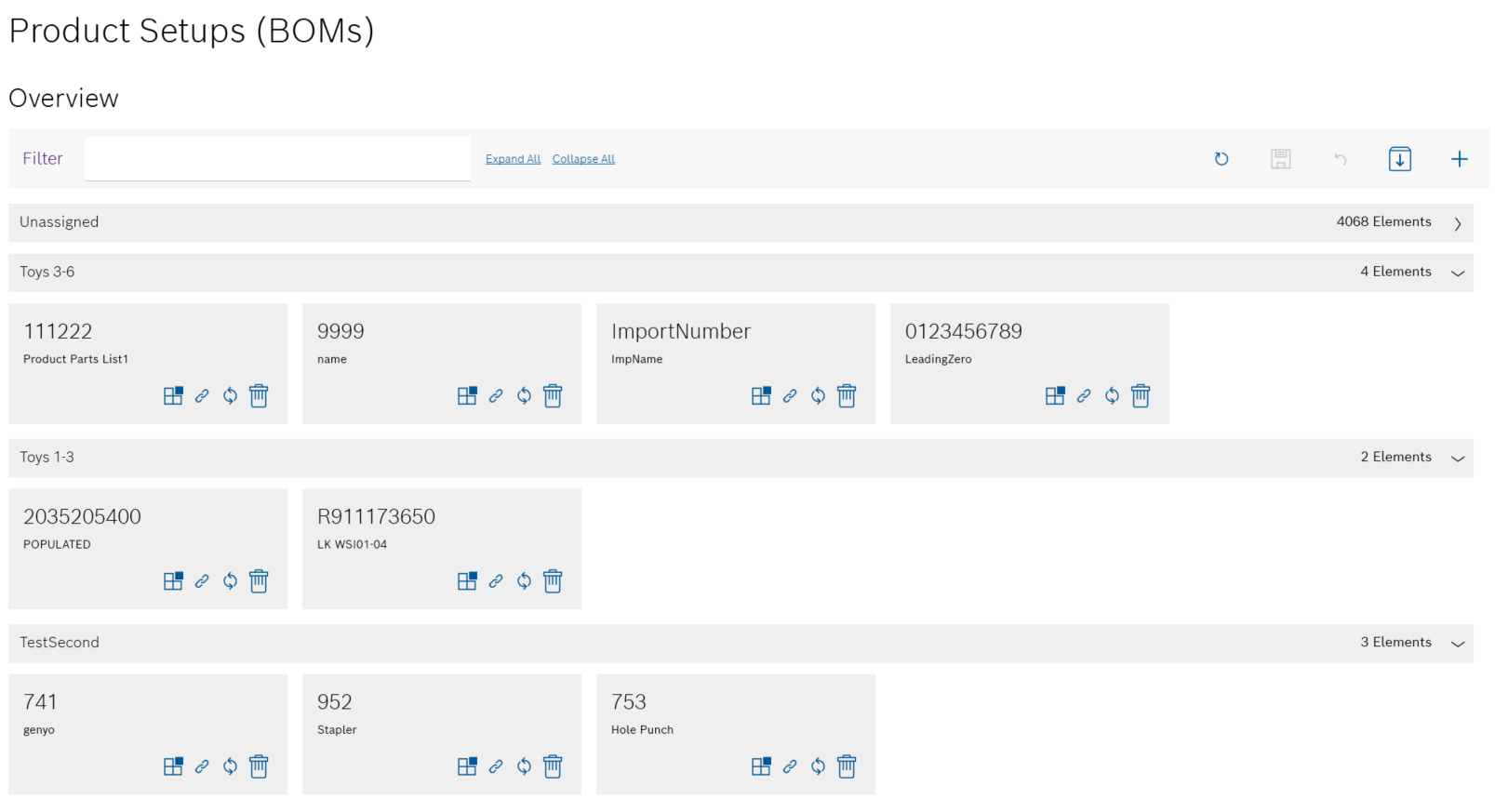
Functions in the overview of product parts lists
Element/icon | Description | ||
---|---|---|---|
Filter |
Search for a product. |
||
Expand all |
Expand all groups of products. |
||
Collapse all |
Collapse all groups of products. |
||
Refresh page. |
|||
Save changes in the overview. |
|||
Undo changes in the overview. |
|||
Import product parts lists. |
|||
Create new product with product parts list. |
|||
Collapse group. |
|||
Expand group. |
|||
Change the assignment of the product to a group. |
|||
If changes are made to the product parts lists in the ERP system, synchronize the product parts lists for the product in the Product Setup Management client.
|
|||
|
Functions in the variants/versions of product parts lists view
To display the product parts lists of a product, click on the product.
Example:
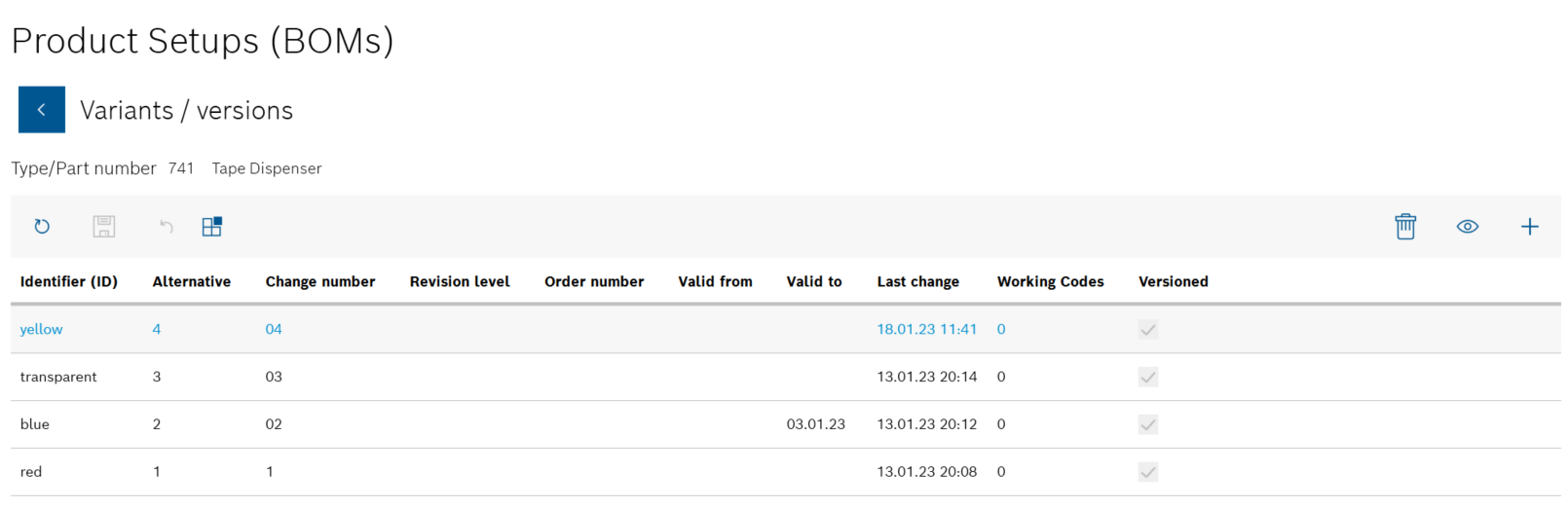
All product parts lists are sorted by Identifiers (ID) in the Variants/Versions view.
Element/icon | Description | ||||
---|---|---|---|---|---|
Go back to the overview of products. |
|||||
Refresh page. |
|||||
Save changes in the Variants/versions view. |
|||||
Undo changes in the Variants/versions view. |
|||||
Change the assignment of the product to a group. |
|||||
|
|||||
Display component and material list of the product parts list.
|
|||||
Create a new product parts list for the product. |
Functions in the component/material list view of product parts lists
Double-click a product parts list to display the components and materials of a product parts list.
Or:
Select the product parts list and open the Component/material list view with .
Example:
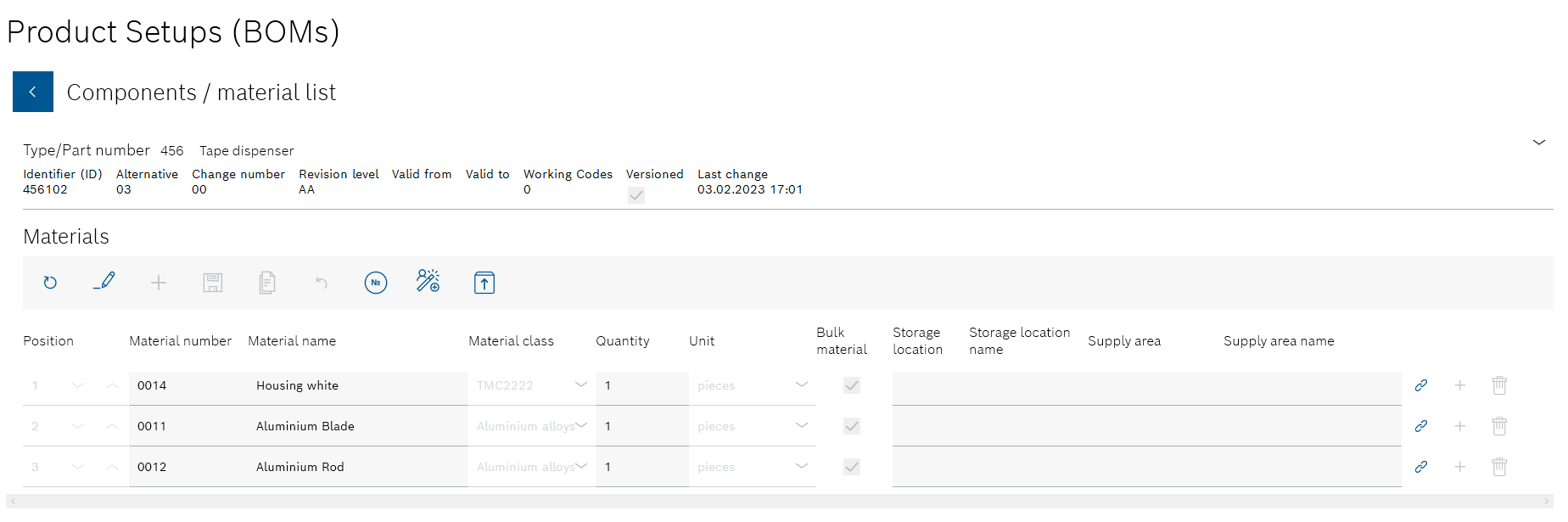
Element/icon | Description | ||
---|---|---|---|
Go back to the Variants/versions view. |
|||
Refresh page. |
|||
Edit the list of components and materials. |
|||
Add a new component or new material to the product parts list. |
|||
Save changes to the product parts list. |
|||
Save changes to the product parts list as a copy. |
|||
Undo the change in the Component/material list view. |
|||
Link production order to the product parts list. |
|||
In the row of a component or a material. |
|||
In the row of a component or a material. Add a subordinate component or subordinate material.
|
|||
In the row of a component or a material. Delete component or material from the product parts list.
|
Create product parts list
A product can be created during the creation of a product parts list. One or more product parts lists can be added manually to each product.
There is no connection to an ERP system when creating a product parts list manually. |
Prerequisite
Expert
or Administrator
role
Procedure
-
Open the Product parts lists menu.
Product parts lists -
If the product is not yet displayed in the overview, open the Add new product parts list dialog window in the overview with
in the header.
The new product is created together with the product parts list.
Or:
If the product to which the new product parts list is to be added is present in the overview, proceed as follows: * Select product. Filter by product if necessary.
+ image::psm_product_setups_versions_2023_01.png[psm_product_setups_versions]
+ All product parts lists for the product are listed in the Variants/versions view.
-
Open the Add new product parts list dialog window in the Variants/versions view with
in the header.
The new product parts list is assigned to the product.
If the product parts list is not to have any variants or versions, uncheck the Versioned checkbox. The relevant input fields are hidden.
A product parts list can be versioned if multiple different variants of the product are produced (e.g. different housing colors).
-
-
Enter the following details:
-
Type/item number
Product identifier -
Type/item name
Name of the product -
Identifier (ID)
Product parts list identifier -
Part type
In the drop-down list, select the part type to which the product parts list is to be assigned.Additional Part types can be created and edited in Master data > Part types.
Master data: Part types
-
-
If the product parts list is to be versioned, activate the Versioned checkbox and complete the following input fields:
: A new version of the product parts list will be created after each change.
: The product parts list can be edited without creating a new version of the product parts list. The input fields that are relevant for versioning are hidden.
-
Alternative
If the product is produced in different variants (e.g. different housing colors), enter a number that identifies the variant. -
Change number
Enter the change number of the ERP system. -
Revision
In the drop-down list, select an indicator that indicates the change status of the product parts list. -
Valid from
Pressto open the calendar and select the desired date.
-
Valid to
Pressto open the calendar and select the desired date.
-
-
Use Add to create the product parts list.
The individual components and materials of the product are listed in the Component/Material list view.
-
Create the individual components and materials of the product parts list:
-
In the header, use
to add a new item number for a component or a material.
-
If necessary, use
next to a component or material to add subordinate components or materials.
The
Administrator
can usenext to a component or material to delete individual components and materials from the product parts list.
-
-
Enter the following data for the relevant component or material:
-
Item number
-
Material number
-
Material name
-
Material class
-
Material classes can be created and edited in Master data > Material classes. |
-
Quantity
-
Unit
-
Storage location
Storage location identifier -
Storage location name
-
Coverage area
Supply area identifier -
Supply area name
-
If the component or material is supplied as bulk material, activate the Bulk material checkbox.
-
Use
in the header to create the product parts list.
-
If the product was not previously available in the overview, the new product is created. The created product parts list is displayed when the product is selected in the Variants/versions view.
-
Continue with Import product parts list from file to import a product parts list.
-
Continue with Link the product parts list to a product assembly plan to add a product assembly plan to the product parts list.
-
Continue with Link the component or material of a product parts list to an action to link a component or a material of the product parts list to an action.
-
Continue with Link product parts list to a production order to link the product parts list to a production order.
Edit product parts list or create a copy as a variant
Depending on the setting of the client, it is possible to save the changes in the open product parts list or to create a variant from it in which the changes are saved. The product parts list that has been edited retains its original data.
When a product parts list is changed manually, there is no connection to an ERP system. |
Requirements
-
At least one product with at least one product parts list has been created.
Create product parts list -
Expert
orAdministrator
role
Procedure
-
Open the Product parts lists menu.
Product parts lists -
In the overview, select the product whose product parts list is to be changed. Filter by product if necessary.
All product parts lists for the product are listed in the Variants/versions view.
-
Select the desired product parts list to be changed.
-
Use
to open the Component/material list view.
All components and materials in the product parts list are displayed.
-
Press
in the header to activate editing.
The data of the product parts list is no longer grayed out and can be changed.
-
If necessary, edit the individual components and materials of the product parts list:
-
If necessary, use
in the header to add a new item number for a component or a material.
-
If necessary, use
next to a component or material to add subordinate components or materials.
The
Administrator
can usenext to a component or material to delete individual components and materials from the product parts list.
-
-
If necessary, edit the following data for the respective component or material:
-
Item number
-
Material number
-
Material name
-
Material class
-
Material classes can be created and edited in Master data > Material classes. |
-
Quantity
-
Unit
-
Storage location
Storage location identifier -
Storage location name
-
Coverage area
Supply area identifier -
Supply area name
-
If the component or material is supplied as bulk material, activate the Bulk material checkbox.
You can use
to link a product parts list to a production order.
Link product parts list to a production order
You can useto link a product parts list to a product assembly plan.
Link the product parts list to a product assembly plan -
Click
in the header to save the changes in the product parts list and confirm with Yes in the dialog window.
No other version of the product parts list is created.
is only available if the client is connected to the ERP system and the original product parts list has been saved as not Versioned.
Or:
is only available if the client is not connected to the ERP system and the original product parts list has been saved as Versioned or not Versioned.
Or:
Use
to save the changed product parts list as a new version.
This does not change the original product parts list.
is only available if the client is connected to the ERP system and the original product parts list has been saved as Versioned.
Or:
is only available if the client is not connected to the ERP system and the original product parts list has been saved as Versioned or not Versioned.
The information from the original product parts list is displayed in the Add new product parts list dialog window.
-
If necessary, edit the following information in the Add new product parts list dialog window:
-
-
Type/item name
Name of the product -
Identifier (ID)
Product parts list identifier -
Part type
In the drop-down list, select the part type to which the product parts list is to be assigned.Additional Part types can be created and edited in Master data > Part types.
Master data: Part types -
If the product parts list is to be versioned, check the Versioned checkbox.
: A new version of the product parts list will be created after each change.
: The product parts list can be edited without creating a new version of the product parts list. The input fields that are relevant for versioning are hidden.
-
Alternative
If the product is produced in different variants (e.g. different housing colors), enter a number that identifies the variant. -
Change number
Enter the change number of the ERP system. -
Revision
In the drop-down list, select an indicator that indicates the change status of the product parts list. -
Valid from
Pressto open the calendar and select the desired date.
-
Valid to
Pressto open the calendar and select the desired date.
-
Use Add to create the new version of the product parts list.
If the changed product parts list has been saved as an additional version, it is displayed in the Variants/versions view of the product. If the changes to the product parts list have been saved, the changed data is displayed in the Component/material list view of the product parts list.
Import product parts list from file
Only files created from a supplied template can be imported as product parts lists. The template can be downloaded, edited and uploaded during the process.
A file can be used for multiple products and multiple product parts lists. |
Prerequisite
Expert
or Administrator
role
Procedure
-
Open the Product parts lists menu.
Product parts lists -
Select
in the header.
-
Select Import from file in the drop-down list.
Download template
The file of a product parts list must be created on the basis of a supplied template. This template can be downloaded, edited and saved under the name of the product parts list in the Import product parts list dialog window.
This step can be skipped if the file of the product parts list has already been created on the basis of a supplied template. |
-
Select the desired template from the Select an import/export template drop-down list.
-
Select Create empty template from the drop-down list.
The template opens as an Excel file.
-
Enter the data in the Excel file and save as a product parts list in the file manager.
Import product parts list
The product parts list is available as a *.xslx file. |
-
Select the template used for the file from the Select an import/export template drop-down list in the Import product parts list dialog window.
-
Click on Select.
The file manager opens.
-
Select and open the product parts list (*.xslx file) in the file manager.
The selected file path appears in the Select a product parts list input field.
-
Use Import to upload the file to Product setup management.
The created products are displayed in the overview. Clicking on each product opens its respective Variants/versions dialog window, in which all product parts lists of the product are listed.
-
Continue with Import product parts list from ERP system to import product parts lists from an ERP system.
Import product parts list from ERP system
With an import, multiple product parts lists can be imported for the same product. |
Prerequisite
Expert
or Administrator
role
Procedure
-
Open the Product parts lists menu.
Product parts lists -
Select
in the header.
-
Select Import from ERP in the drop-down list.
-
Enter the following details:
-
Type/item number
Enter the product identifier. -
Revision
In the drop-down list, select an indicator that indicates the change status of the product parts lists.Or:
Validity date
Useto open the calendar and select the desired date from which the product parts lists are valid.
-
-
Click Add to import the product parts lists from the ERP system.
The product parts lists are imported from the ERP system and listed in the Variants/versions view of the product.
-
Continue with Import product parts list from file to import product parts lists from a file.
Group products and packaging specifications or change grouping
Products and packaging specifications can be displayed in groups in the overview. Individual products and packaging specifications can be assigned to a group and the grouping can be changed.
The products and packaging specifications are grouped in the overviews of the Product parts lists , Product assembly plan and Packaging specifications menus to make them easier to find.
Groups can be created in Master data > Groupings and multiple products can be grouped at the same time. |
Prerequisite
Expert
or Administrator
role
Procedure
-
Open the Product parts lists, Product assembly plan or Packaging specifications menu.
Product parts lists
Product assembly plan
Packaging Instructions -
In the product or in the packaging specifications, open the Add to grouping dialog window with
.
Type/item number and Description cannot be changed.
-
Select the required group in the Grouping drop-down list.
-
Apply the input with Save.
Example:
A bar with the group name is displayed above the grouped products and packaging specifications. You can use
to collapse individual groups.
In the header, the groups can be expanded using Expand all and collapsed using Collapse all.
The product or packaging specifications are listed in the overview under the desired group.
-
Continue with Create a new group to create groups.
-
Continue with Edit group to assign multiple products to a group.
Link product parts list to a production order
A product parts list that has already been created can be linked to the number of a production order.
The information is opened by the Order Management module. |
Requirements
-
At least one product with at least one product parts list has been created.
Create product parts list -
Expert
orAdministrator
role
Procedure
-
Open the Product parts lists menu.
Product parts lists -
Select the product whose product parts list is to be linked to the production order. Filter by product if necessary.
All product parts lists for the product are listed in the Variants/versions view.
-
Select the desired product parts list to be linked to the production order.
-
Use
to open the Component/material list view.
-
Use
to open the Link to order dialog window.
-
Enter the number of the production order to which the product parts list is to be linked in Order number.
-
Apply the link with Save.
Any number of production orders can be linked to the product parts list by clicking
again.
The order number of the production order is displayed in the Order number column in the Variants/Versions view.
Link the product parts list to a product assembly plan
A product parts list that has already been created can be linked to a product assembly plan.
The type/item number of the product parts list and the product assembly plan must be the same. |
Requirements
-
At least one product with at least one product parts list has been created.
Create product parts list -
At least one product assembly plan has been created.
Create product assembly plan -
Expert
orAdministrator
role
Procedure
-
Open the Product parts lists menu.
Product parts lists -
Select the product whose product parts list is to be linked to a product assembly plan. Filter by product if necessary.
All product parts lists for the product are listed in the Variants/versions view.
-
Select the desired product parts list to be connected to the product assembly plan.
-
Use
to open the Component/material list view.
-
Use
to open the Component/material assignments view.
is only displayed if a product assembly plan with the same Type/item number has been created.
Create product assembly planThe details of the generated product assembly plan are displayed in the upper area of the Component/material assignments view. In the middle area Lines , you can select the lines and stations to which the components and materials are assigned in the lower area Assignment. The name of the line selected in the Lines area and the station is displayed in the Assignments area.
Product assembly plan -
Select the line and station of the line to which the components and materials of the product parts list are to be assigned:
-
In the Lines area, select a line from the drop-down list.
-
In the Lines area, select a station of the selected line from the table.
The name of the line selected in the Lines area and the station is displayed in the Assignments area. The Product parts list area appears on the right-hand side.
-
-
In the Product parts list area, select the product parts list that the components and materials are to be assigned to the station from.
Only one product parts list can be used for the product assembly plan. Components and materials from different product parts lists cannot be assigned in the same product assembly plan.
The Lines and Product parts list areas are automatically collapsed. The Materials area appears on the right under the Product parts list area with the abbreviation of the selected product parts list: <Typ-/Sachnummer>-<Alternative>-<Change number> (date and time of the last change).
All components and materials of the selected product parts list are displayed in the Materials area.
-
Assign the required components and materials to the selected station:
-
Drag and drop the component or material from the Materials area to the Assignments area.
To remove a component or material from the assignment of the station, the
Administrator
can select the component or material in the Assignments area and delete it in the header of the area using.
-
-
If necessary, switch between the lines and their stations:
-
Use
in the Lines area to open the lines and their stations.
-
Select the desired line from the drop-down list in the Lines area.
-
Select the desired station of the line from the table in the Lines area.
The name of the line selected in the Lines area and the station is displayed in the Assignments area.
The components and materials of a product parts list can be assigned to any number of stations.
-
-
Link the product assembly plan using
in the header of the Assignments area.
The information about the product assembly plan is displayed in the Add new product assembly plan dialog window
-
If necessary, edit the following information in the Add new product assembly plan dialog window:
-
Assembly plan name
Enter the product assembly plan identifier. -
Range
Enter the location of the lines at which the components and materials are to be processed. -
Production version
Select the production version from the drop-down list. -
If the product assembly plan is to be versioned after changes, activate the Versioned checkbox.
: A new version of the product parts list will be created after each change.
: The product parts list can be edited without creating a new version of the product parts list.
-
If necessary, use Parameters
to create new parameters.
Input fields appear under Name and Value to define the parameters.You can use
to add up to ten parameters to the product assembly plan.
The parameter can be deleted usingin the row of a parameter.
-
Under Available lines , activate the checkboxes of the lines on which the components and materials can be processed.
This entry cannot be undone. If the components and materials are additionally assigned, only the lines selected here can be chosen.
-
Use Add to link the product parts list to the product building plan.
-
image::psm_product_building_plan_add_new_components_result_2023_01.png[psm_product_building_plan_add_new_components_result]
The product parts list is linked to the product building plan. All lines and stations with the assigned components and materials are displayed in Product assembly plan in the Component/material assignments view.
Link the component or material of a product parts list to an action
If components or materials of a product parts list must meet certain criteria before they are packed, they can be linked to actions. These actions contain parameters that must be complied with when checking the component or material (e.g. measurement types, units of measurement, tolerance limits).
The data for the respective action can be opened with the component or the material for further processing from the Packaging Control client and, if applicable, from additional modules.
Actions can be created and edited in Master data > Actions. |
Requirements
-
At least one product with at least one product parts list has been created.
Create product parts list -
Expert
orAdministrator
role
Procedure
-
Open the Product parts lists menu.
Product parts lists -
In the overview, select the product in whose product parts list a component or a material is to be linked to an action. Filter by product if necessary.
All product parts lists for the product are listed in the Variants/versions view.
-
Select the desired product parts list in which a component or material is to be connected to an action.
-
Use
to open the Component/material list view.
All components and materials in the product parts list are displayed.
-
Click
in the row of the desired component or material.
All available actions are listed in the Link to action dialog window.
-
Activate one or more checkboxes of the desired actions that are to be linked to the component or material.
-
Apply the link using Save.
The component or material is linked to the action. All products, components and materials that are linked to an action can be displayed in Type/material actions.
Type/Material actions
-
Continue with Link product to an action to link a product to an action.
Link product to an action
If products have to meet certain criteria before they are packed, they can be linked to actions. These actions contain specific data that must be complied with when testing the product (e.g. measurement types, units of measurement, tolerance limits). The data for the respective action can be opened with the product for further processing from the Packaging Control client.
Actions can be created and edited in Master data > Actions. |
Requirements
-
At least one product is created.
Create product parts list -
Expert
orAdministrator
role
Procedure
-
Open the Product parts lists menu.
Product parts lists -
Click
in the overview within the desired product. Filter by product if necessary.
All available actions are listed in the Link to action dialog window.
-
Check one or more checkboxes of the desired actions that are to be linked to the product.
-
Apply the link using Save.
The product is linked to the action. All products, components and materials that are linked to an action can be displayed in Type/material actions.
Type/Material actions
-
Continue with Link the component or material of a product parts list to an action to link a component or a material of the product parts list to an action.
Export product parts list
Individual product parts lists can be opened and downloaded as *.xlsx files in Excel.
Requirements
-
At least one product with at least one product parts list has been created.
Create product parts list -
Expert
orAdministrator
role
Procedure
-
Open the Product parts lists menu.
Product parts lists -
Select the product whose product parts list is to be downloaded. Filter by product if necessary.
All product parts lists for the product are listed in the Variants/versions view.
-
Select the desired product parts list to be downloaded.
-
Use
to open the Components/materials list view.
All components and materials in the product parts list are displayed.
-
Use
to open the Export product parts list dialog window.
-
Select the desired template to which the data of the product parts list is to be transferred in the Select template drop-down list.
-
Open the .xslx file with
*Export.
The data of the product parts list is opened in an Excel file. The file can be saved.
-
Continue with Import product parts list from file to import a product parts list from an Excel file.
Delete product parts list
Individual product parts lists of a product can be deleted.
The deletion process must be saved in the Variants/versions view. |
Requirements
-
At least one product with at least one product parts list has been created.
Create product parts list -
Administrator
role
Procedure
-
Open the Product parts lists menu.
Product parts lists -
Select the product whose product parts list is to be deleted. Filter by product if necessary.
All product parts lists for the product are listed in the Variants/versions view.
-
Select the desired product parts list to be deleted.
Additional tools appear in the header.
-
Use
in the header to delete the selected product parts list.
-
Click Yes in the dialog window to permanently delete the product parts list.
-
Click
to save the change in the Variants/versions view.
You can undo the deletion by clicking
before the change is saved in the Variants/versions view.
The product parts list is no longer displayed under the product in the Variants/versions view.
-
Continue with Delete a product with product parts lists to delete a product with all its product parts lists.
Delete a product with product parts lists
Products can be deleted with all the included product parts lists.
The deletion process must be saved in the overview. |
Requirements
-
At least one product with at least one product parts list has been created.
Create product parts list -
Administrator
role
Procedure
-
Open the Product parts lists menu.
Product parts lists -
Click
in the product to be deleted.
-
Select Yes in the dialog window to permanently delete the product and all product parts lists of the product.
-
Click
to save the change in the Overview.
Before the change is saved in the Overview , you can undo the deletion by clicking
.
The product is no longer displayed in the overview of the product parts lists.
-
Continue with Delete product parts list to delete an individual product parts list.